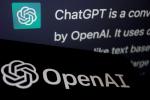
Please try another search
The pace of change in the energy industry is growing significantly. The industry is being turned on its head by the shale revolution sweeping across North America. Abundant supply of natural gas from domestic production is making North America a magnet for manufacturing returning from offshore attracted to low natural gas prices. But low prices are squeezing producers. Energy infrastructure built for a conventional world is being turned on its head by the unconventional shale revolution can easily be either in the wrong place or flowing in the wrong direction to bring onshore oil and gas to market.
The shale revolution is not limited to North America but it is booming there first as favorable geology, private property rights, access to advanced technology and expertise and other factors change market behaviors in search for a new equilibrium. The abundant supply of natural gas has driven down prices putting pressure on producers to control costs, shift production from dry gas to more profitable natural gas liquids or expand exports—or all of the above. Higher prices for natural gas liquids create a pull to capture profits from these critical commodities even if doing so increases the dry gas supply. The global competition for energy is converting traditional regional markets for natural gas into global markets as excess supply turns into exports of LNG chasing higher prices in Asia and elsewhere.
Canada is a source for much of the imported natural gas to US markets. Oil sands from Canada also need access to US energy infrastructure to find the way to markets after processing. The question is whether the same shale revolutionary forces that changed natural gas markets so profoundly will do the same to oil markets. US Shale development worries Canadians as their resources face competition from growing US domestic supplies. The search for market equilibrium in rapidly changing oil and gas markets is forcing many firms to rethink strategies, improve field operations, expand flexibility and use managed services contractors to optimize performance and control chemical and operating costs (OPEX).
The intensifying focus on field performance and rapid response field data gathering is systematically changing every firm’s performance optimization strategy. The challenge at the front line of oil and gas production is to proactively manage operating costs to assure profitability in the low natural gas price environment in North America, keep production running smoothly and reliably to enable exports of abundant supply where that makes sense, and assure that capital invested in plant and equipment is maintained and utilized to create shareholder value.
Controlling operating costs and improving performance profitability forces field superintendents to ask:
How do we get field data essential to monitor well operations into the hands of field crews in remote locations to assure production?
Field performance optimization starts at the well site by gathering and leveraging the data available from regular inspection and monitoring to identify operations problems that can interfere with production. For field operators this is often difficult to do:
Pattern analysis of gathered field and equipment operating data over time provides valuable predictive analytics insight into possible equipment failure or well shut downs to avoid equipment replacement at costs of hundreds of thousands of dollars. Avoiding costly work-overs is critical to performance optimization at the front lines. Assuring high quality field performance requires systematically capturing field data and using it to take action, often on the spot, to keep equipment running within normal tolerances, adjust chemical injections to optimize performance and minimize cost. The OPEX cost savings from reduced chemical use and avoiding expensive work overs when failure happens are the most practical and profound ways of optimizing field performance at a given well, across a field or division and then across the enterprise. Aggregating this field data and using fast, easy and reliable visual data analysis technology can quickly provide insight to improve production. This isn’t rocket science but it does require a systematic business process, clear key performance indicators routinely measured and the tools and trained talent to gather, assess and rapidly respond to the real-time or near real time data on well or field performance.
CASE STUDY 1: GETTING METHANOL INJECTION RATES RIGHT
At a large natural gas production company a recent field trial focused on reducing field operating costs from the injection rates for methanol. Survey of typical well field operations showed methanol injection rates were often set as the well went into production when output was highest. Limited staff and vendor contract deliveries of methanol meant that not as much attention was paid to adjusting methanol injection rates over time as well production settles down. The result was that methanol was often being over injected in many of the wells surveyed driving up the cost of operations.
The field data gathering solution used in this trial was HotLeap TRACKERTM from Hot Button Solutions, a Calgary-based field services technology company. The HotLeap product uses a rugged handheld device to allow field crews to gather temperature, pressure and other readings as they make their inspection rounds. It was used to take field trial methanol injection rate readings to assess opportunities to reduce OPEX by alerting crews to match methanol injection rates to well production.
When a well comes on stream methanol is injected so pipelines don’t freeze and is often over-injected initially until the well operates normally. Production rates start out strong, flatten out within a few months and then slowly decline. On older wells production declines at a normal rate of 8 to 10%.
It is easy to waste thousands of dollars in methanol over-injection driving up operating costs and reducing well profitability. Tracker helps monitors injection rates by alerting field crews to dial-back methanol to match production and validate the adjustment results with accurate injection rate time series data. The figure below shows an all too common problem. The blue bars show the current injection rates for methanol at the sample of 16 well sites tested. The dark maroon bars show the actual level of methanol injection required at each of the well sited tested. Methanol is delivered by contract vendors directly to the well sites. The vendors are paid 62 cents/liter for the methanol which prevents hydrate formations that freeze the wells and cause major damage to equipment.
Chemical injection of corrosion inhibitors is a common way to control corrosion in a pipeline. The process of corrosion inhibition is due to the adsorption of the inhibitor on the pipe wall to form a hydrophobic layer that prevents water from contacting the pipe wall. Adsorption is defined as the adhesion of atoms, ions, or molecules from a gas, liquid, or dissolved solid to a surface. Adsorption differs from absorption, in which a fluid is dissolved by a liquid or solid. Adsorption is a surface-coating of the material as a protectant against corrosion. Getting corrosion inhibitors to work requires precise calibration of the amount of chemical inhibitor concentration needed to produce the desire adsorption effect. Add too much chemical and it is wasted since more is not necessarily better protection. But add too little and the chemical reaction is not sufficient to provide the desired corrosion protection thus damaging the pipe and still wasting money.
Monitoring inhibitor levels in a pipeline can be done by measuring the inhibitor concentration in the produced fluid. But this can be labor intensive and the cost of automated equipment in large field operations is impracticable. Contract vendors are often used to deliver chemical inhibitor with periodic sampling done to adjust injection levels in a process similar to the earlier methanol case study.
Since vendors delivering corrosion inhibitor only sample wells to assess injection rates exposure to higher costs from over injection is material. But the risk from under injection is a bigger problem since under injection does not adequately protect the pipeline or the well. This means the cost of the injected inhibitor is wasted as ineffective and the pipeline or well is left exposed to corrosion and future repair or failure. The field trial did not cover all 260 wells in the sample field. But of the 18 sampled the savings potential from better management of corrosion inhibitor injection was found to be $205,860 per well annualized.
The Bottom Line
There is substantial opportunity for operating expense cost reduction, improved well and field operating performance and better production management by making cost effective use of field data gathered and integrated into a performance optimization management plan for field crews and vendors. The easy availability of cost effective solutions like HotLeap Tracker used in these field trials demonstrated the benefits clearly.
Aggregated field data gathered across the portfolio or enterprise provides a real-time or near real time rapid response feedback loop for preventive maintenance and performance optimization. Leveraging the field data gathers and providing a knowledge base of critical information and insight into needed inspection and injection rate adjustments to be performed by the field crews or as part of a managed services contract with vendors offers real potential for improved operating performance, reduced cost and enhanced shareholder value.
The silver market is forecast to record a fifth straight market deficit in 2025, with demand once again outstripping supply, and the majority of the existing above ground silver...
Trumping Brent Oil Futures. Oil got Trumped and dumped. While many people feared that President Trump aggressive trade negotiations would raise the price of oil, so far oil has...
Upon analysis of the wobbly moves since Tuesday, when the natural gas futures tested the two-year high at $4.55, Thursday might be a cozy one, as the inventory announcements after...
Are you sure you want to block %USER_NAME%?
By doing so, you and %USER_NAME% will not be able to see any of each other's Investing.com's posts.
%USER_NAME% was successfully added to your Block List
Since you’ve just unblocked this person, you must wait 48 hours before renewing the block.
I feel that this comment is:
Thank You!
Your report has been sent to our moderators for review
Add a Comment
We encourage you to use comments to engage with other users, share your perspective and ask questions of authors and each other. However, in order to maintain the high level of discourse we’ve all come to value and expect, please keep the following criteria in mind:
Enrich the conversation, don’t trash it.
Stay focused and on track. Only post material that’s relevant to the topic being discussed.
Be respectful. Even negative opinions can be framed positively and diplomatically. Avoid profanity, slander or personal attacks directed at an author or another user. Racism, sexism and other forms of discrimination will not be tolerated.
Perpetrators of spam or abuse will be deleted from the site and prohibited from future registration at Investing.com’s discretion.